Medtec China模具设计手册:复合材料锥壳成型模设计
2023-07-25
1 复合材料热压罐成型工艺
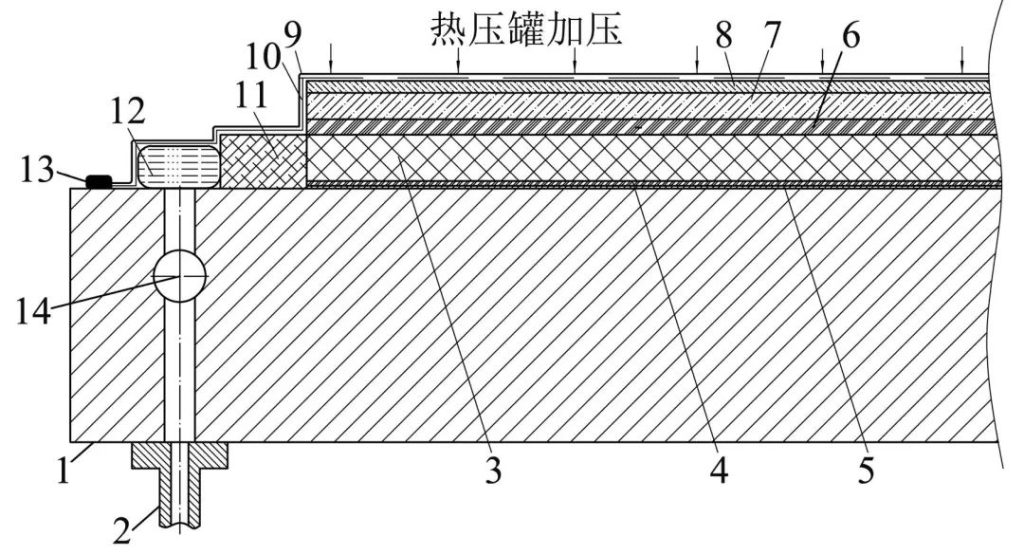
1.平板模具 2.接真空源 3.制品 4.隔离层 5.脱模层 6.分离层 7.均压板 8.透气毡 9.真空袋 10.透气层 11.柔性挡块 12.排气材料 13.密封胶条 14.排气导管
2 碳/环氧锥壳
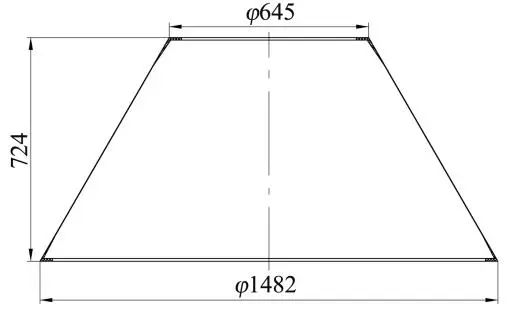
3 模具结构
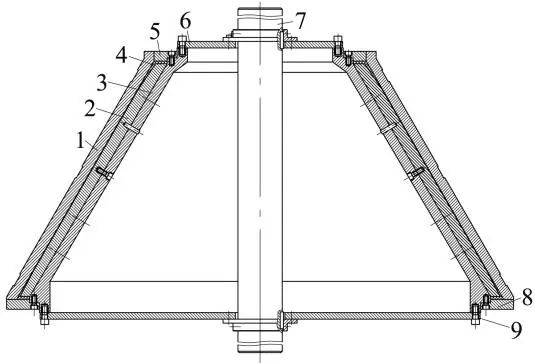
1.凹模 2.凸模 3.芯模 4.制品 5.上压环 6.上法兰 7.轴 8.下压环 9.下法兰
4 模具主要零件材料选择
Medtec China已经吸引了来自上海发那科、宁波长飞亚塑料机械制造、东莞吉达优、峰锐精密工业、昱高精密制造、纳托模塑系统、上海超日、东江模具、汉匠模具科技将带来塑模成型等相关产品及服务。
4.1 凸模材料的选择
4.2 其它主要模具零件材料的选择
5 模具设计时需注意的问题
5.1 模具膨胀问题
5.2 凸模分瓣问题
5.3 模具零件间隙的问题